Raymond Mill
Home products
Powder making machine
Raymond Mill
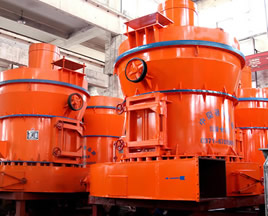
Raymond Mill
- High grinding efficiency
- Low energy consumption
- Smaller floor area
- Low investment
Introduction to Raymond Mill
Raymond mill is designed by adopting advanced structure of similar products at home and abroad and bettering them in the industry. It has higher grinding efficiency and lower energy consumption, smaller floor area and investment than that of the ball mill.
The long replacement cycle of the grinding roll and the grinding ring eliminates the shortcomings of the centrifugal crushing machine. The winnowing airflow of the machine works circularly from the draught fan, to the mill shell, cyclone separator and then back to the draught fan again. Therefore, the dust is less than that produced by the high speed Centrifugal Crusher, resulting in a clean operating workshop without polluting the environment.
Main Structure of Raymond Grinder
The Raymond mill is mainly made up of the host, analyzer, blower, finished product cyclone separator, micro powder cyclone separator and air pipe. Among them, the host is made up of the frame, the volute for the wind getting in, the relieving knife, the grinding roll, the grinding ring and the housing.
Application Scope of Raymond Grinding Mill
Hongxing Raymond mill is widely used for materials with Mohs hardness less than the magnitude of 9.3 and humidity below 6%, such as barite, calcite, potassium feldspar, talc, marble, limestone, dolomite, fluorite, lime, activated clay, activated carbon, bentonite, kaolin, cement, phosphate rock, gypsum, glass, thermal insulation materials, etc. It is applied in industries like mining, chemical industry and architecture for highly fine power processing. The granularity can be adjusted from 80 to 325 meshes, some can even reach 600 meshes.
Winnowing Process of Raymond Mill
After the materials are ground, the host will inhale the wind into the cabinet inside the host for blowing powder. The powder is separated by the analyzer above the grinding chamber, with the over-thick materials being crushed again in the grinding chamber and the qualified materials getting into the cyclone collector following the wind. After collected, the materials are discharged by the powder discharge port as finished products.
The current returns to the draught fan from the return air duct on top of the large whirlwind collector. It forms a circular path and flows under negative pressure. The extra wind will be discharged from exhaust pipeline between the draught fan and the host to the small whirlwind collector for purification treatment.
When working, the to-be-crushed materials are added to the machine from the feeding port on the side of the housing. Relying on the grinding roller device hanging on the plum flower frame on the host, it revolves around the vertical axis during its self rotation. Due to the role of rotating centrifugal force, the grinding roll swings outside, tightly pressing the grinding ring, moving the materials scooped up by the shovel knife to the place between the grinding roller and grinding ring, and thus the purpose of crushing materials can be achieved.
Model | 4525 | 4119 |
Feeding Size(mm) | ≤30 | ≤25 |
Output Size(mm) | 0.173-0.044 | 0.173-0.044 |
Shift Output of Different Material Fineness(t) | 16-176 | 8-78 |
Rotation Speed of Central Shaft(r/min) | 82 | 105 |
Ring Diameter(mm) | 1770 | 1400 |
Roller Diameter(mm) | 450 | 410 |
Roller Height(mm) | 250 | 190 |
Main Motor(kw) | Y315M-4-132 | Y280S-4-75 |
Fan Motor | Y315M-4-132 | Y280S-4-75 |
Analyzer Motor | YCT250-4A-18.5 | YCT200-4B-7.5 |
Note: If you're interested in the product, please submit your requirements and contacts and then we will contact you in two days. We promise that all your informations won't be leaked to anyone.